hard-wearing, soft and adaptable to temperature changes. It has different features according to which part of the animal’s body it is taken from. Before processing, the hide is divided in two parts: the exterior, known as “grain leather” and the interior known as “split leather”. Grain leather is smooth, flexible and resistant to humidity (this is its primary function in nature) and is the best choice to guarantee good dexterity and sensitivity. Split leather, which has a rougher surface and is resistant to heat, is used for more heavy-duty tasks and where good thermal insulation is required (e.g. welding) and in wet, greasy and oily environments for its excellent grip.
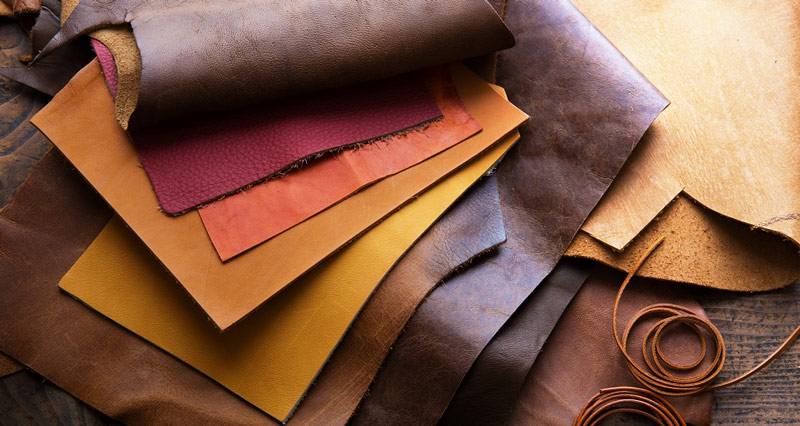